New IWASHO、製袋業界の明るい未来へ 〜 DXで自動化・合理化を推進
製袋機メーカーの(株)New IWASHO(本社/愛知県あま市、氷上好孝社長)は、40年前から自動化・合理化が進んでいないという製袋業界の現状を危惧し、製袋業界の明るい未来に向けて、DXを活用した様々なシステム・周辺機器を開発している。「製袋業界の未来を変えていきたい」というのが氷上社長の想いだ。同社のシステムを使用すれば、製袋作業の失敗によるフィルムの廃棄量も大幅に削減できるため、SDGsにも寄与する。令和時代に相応しい新たな業界基盤の構築を目指す。
同社は元々、1948年に(株)岩正織機製作所として設立したのが始まり。1975年に(株)岩正に称号変更し、ここから製造の中心が織機から製袋機に移行した。
転機となったのは8年前の2014年。画像処理メーカーのダックエンジニアリング(株)(本社/京都市南区、氷上好孝社長)が同社の筆頭株主となり、社長に就任したことである。氷上社長は「ダンボールやオフセットなど、様々な業界を見てきたが、こんなに合理化が進んでいない業界はないと感じた」と製袋業界の将来を危惧したという。
その後、2016年に社名を現在の「(株)New IWASHO」に変更。ダックエンジニアリングで培った技術も融合させながら、昭和の時代からストップしたような製袋業界を令和時代に相応しい業界に変革させるため、最新のDXを取り入れながら、自動化・合理化、見える化を実現するシステムの開発に乗り出した。
利益創出と属人化の問題解決、SDGsにも寄与する製袋機を提供
同社のメーカーとしてのコンセプトは「お客様の期待を超える装置開発と、装置・サービス・情報の提供により、お客様の利益に貢献する」。革新的な技術で製袋機の未来を変えることを使命としている。
製袋業界における作業の難しさについて、「少子高齢化で若者が入ってこないのも製袋業界の課題だが、その原因の1つに自動化が進んでいないため、すべて手作業で行わなければならず、調整が難しいという問題がある。仕事を始めて2〜3年ではとても技術を身に付けることはできない」として、自動化の必要性を強調する。そして、同社では製袋作業の自動化により、キャリアが浅くても十年選手のベテランと同レベルの作業を可能にし、属人化の問題も解決する様々なシステム・周辺機器を開発している。
まず、自動移動システム「posimo(ポジモ)」は、生産品種ごとにシールユニットの位置を記憶し、選んだ品種の設定位置にシールユニットを自動で移動するというもの。製袋の段取りをしている間に移動できるため、段取り時間の大幅な短縮を実現でき、生産性向上を実現する。「オペレーターの作業負荷軽減とスキルレス化に貢献できる装置」と自信を示す。マークセンサの位置を移動させても自動でシールユニットが追従するため、図柄に対してシール位置がずれることもない。
そして、製袋機でのフィルムのシールは、圧力・時間・温度で決まる。その中の圧力・時間を世界初の圧力波形で表示、可視化した装置が、ヒータ圧力センサ計測システム「atu2(アツアツ)」である。ヒータのゴム台に圧力センサを複数埋め込み、生産中、センサにかかる圧力を監視しながらモニターに圧力の波形・数値を表示、ログを残す。
さらに、温度を表示・可視化した装置が、フィルム温度監視システム「Thermon(サーモン)」である。サーモグラフィカメラでフィルム転写熱を監視し、異常があればお知らせ、ログも残す。「重要なのは熱板の温度ではなく、フィルムの温度。いかにフィルムに温度を伝えて樹脂を融かすかが問題」と指摘する。
そして、氷上社長が「他業界にいたからこそ気がつくことができた」というのが、ゲート式自動蛇行ピッチ制御装置「GDP-T」だ。エリアカメラと可動ローラでピッチ・蛇行を自動制御。ドライブ中のテンション監視機能も搭載しており「従来の製袋機をマニュアル車とするなら、これを搭載した製袋機は自動運転を搭載した自動車のようなもの」と氷上社長。さらに、ダックエンジニアリングの画像検査装置「Coco!センサー」と組み合わせれば、蛇行・ピッチ制御と全面検査が同時に行える。
TOKYO PACK 2022に出展
同社は今年10月に東京ビッグサイトで開催される「TOKYO PACK 2022」に出展する。その出展のメインとなるのが、全自動不良排出機能付 集積&帯掛&箱詰装置「SOROERU(そろえ〜る)-H3」である。ロボットアームを使用し、製袋カット後の集積・帯掛け・箱詰めまでを全自動化する。前取り作業を徹底的に自動化することで、省人化・ショット数アップ・人的ミスの軽減に効果を発揮する。
「このような作業はこれまで人手に頼っていたが、未来の高速製袋機に向けて、人手の作業ではとても製袋機のスピードには追いつかない。製袋業界を変革できるシステムであると自負しており、将来的な普及に大きく期待している」(氷上社長)
また「軟包装業界の利益確保につながる」としているのが、 2画面静止画像装置「EYE Vision W」(ダックエンジニアリング(株)製)だ。印刷機・ラミネート・巻替検品機の検反部に設置可能で、シート両端の見当マーク・目印を同時に撮像することで、左右のズレをリアルタイムでモニターに表示して装置を調整、左右のズレの少ない製袋フィルムにより、段取り時間の短縮と製袋不良の削減、ショット数アップに貢献する。
氷上社長は「軟包装業界ではフィルム成膜から印刷・ラミネート等の加工を行い実際に製袋製品となるのは50%とお客様から聞いている。半数を廃棄する原因のひとつは、フィルムの左右がずれた印刷製袋フィルムによる製袋時でのシワ・カール不良が発生することにある。産廃をなくすことにより、SDGsにも寄与する」としており、不良品を作らないという問題は、軟包装業界全体で取り組まなければならない課題であると強調している。
「包む」で社会に貢献へ
氷上社長は「製袋業界に入ってくる若者は少ない。若者たちが触ってみたい、携ってみたいと思える製袋機、また、未来に向かって人に優しいファクトリーオートメーションを実現する製袋機の開発に努力したい」と展望する。
同社は歴史ある製袋機の技術とダックエンジニアリングの革新的な画像処理技術を融合し、明るい未来が見える製袋業界のために製袋機と周辺システムを開発・製造していく。製袋業界全体の発展を目指した取り組みを進める同社に期待したい。
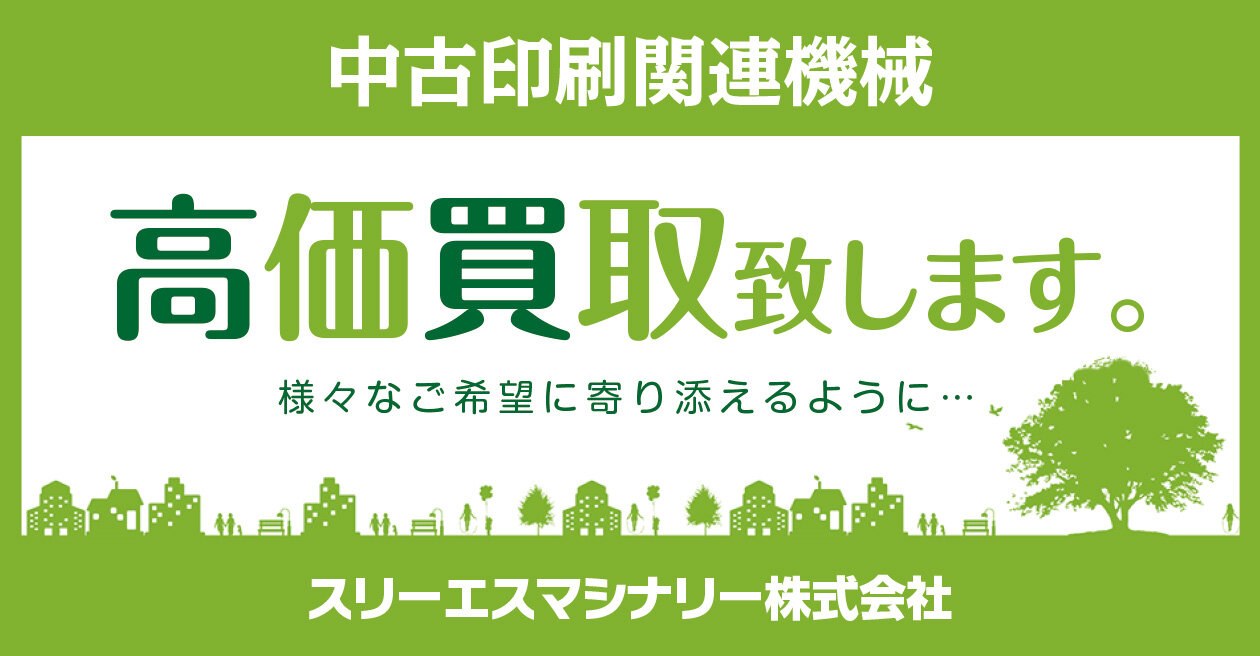