ゴードー、パッケージ印刷分野で「刷版の無処理化」- G段印刷で新市場創出
[SONORA採用事例]予備版削減でコストメリット
パッケージ印刷分野での完全無処理化
新事業領域への挑戦に乗り出した同社は、同時に生産工程の見直しも進めた。そのひとつが「刷版工程の無処理化」である。その資材として同社が選択したのがコダックのプロセスフリープレート「SONORA CX2」だ。
ただ、パッケージ印刷分野における刷版工程の無処理化は、商業印刷分野ほど進んでいないのは周知の事実だ。「水幅」「耐刷」「機上現像による印刷機への影響」といった点に懸念はなかったのか。
まず「水幅」について印刷オペレータで製造部の小山和仁係長は、「SONORAでのテスト印刷において、従来使用していた有処理版との比較でとくに違和感は感じなかった。SONORA自体の性能改善も寄与していると思う」と説明する。
一方、コダックが提示する耐刷スペックは、プロセス4色のパッケージ印刷で5〜6万枚。ただ、金、銀、白、蛍光ピンクといった特色の場合、インキ成分的にプレートへのアタックが強いため、「2万枚あるいはそれを下回るケースもある」としている。およそ6割が特色の仕事だという同社だが、小ロット受注にシフトしていることもあり、平均ロットは5,000枚程度で、2万通し以上の仕事はそれほど多くなく、問題の範疇ではなかった。逆にテスト段階ではプロセス4色で従来使用の有処理版の倍程度の耐刷性を確認できたという。
そして「機上現像による印刷機への影響」については、印刷機に湿し水濾過装置を設備して対応。この点について製造部の菊池由修課長は、「完全無処理版の問題点として当初から危惧されている点だが、SONORA CX2の性能改善によって当社では問題ないと判断している」と説明する。
2つの異なるサイズのプレートを月およそ1,000版出力している同社では、昨夏から新規の仕事をSONORA CX2で、リピートの仕事を有処理版で出力しながら、これらを混在させた形で2ヵ月程度運用し、徐々に移行を進めた。プロセス4色に関しては、リピート物をSONORA CX2でも出力して色見を確認。トーンカーブを2回程度調整することで色合わせ作業を行い、有処理版の在庫を使い切った昨年10月、SONORAへ完全移行している。
「刷版の完全無処理化による工程のスキルレス化、あるいは現像工程に起因するトラブルの排除など、当社が直面していた問題をクリアできたことは大きな収穫だった」(橘社長)
コスト削減と省人化の効果
「刷版工程の無処理化」において、何ら障害がなかったといえる同社。今となっては「無処理化を拒む理由はなかった」(橘社長)と明かす。品質についても「仕事の8割がリピート物だが、クライアントからのクレームは一切ない」と小山係長。逆に「網点がシャープに再現され、品質は向上した。とくにハイライト部分の網点再現性は有処理版を上回る」と証言している。
「刷版工程の無処理化」は、コスト面でも経営に大きく寄与している。同社の現像液とガム液の購入金額は、年間(2021年)で78万円。さらに廃液処理コストは年間26万円。この計100万円強のコスト抑制効果を弾き出している。
コストメリットはこれだけではない。同社では、これまで2万枚以上の仕事の場合、予備版を用意していた。「印刷出身ではない私は、いつも使わないこともあるこの予備版がもったいないと感じていた」と菊池課長。前述の通り、同社が定義するSONORAの耐刷は3万枚であるため、予備版が必要な仕事は3〜4割程度減っている。例えば、月に2万枚以上の仕事が5ジョブあったとする。1版1,500円として4色分で6,000円。この5回分で3万円となり、予備版だけで年間48万円程度のコスト削減効果が期待できる計算になる。
一方、同社ではSONORAへの移行で現像機のスペースが不要になったことから、CTPを印刷工場内に設置している。「これまではスペースの問題でオフィス側の建物の一室にCTPがあり、印刷工場まで3つの扉を開けて運んでいた。これが版キズの原因にもなっていた」(菊池課長)。さらに、SONORA採用にともない導入したCTPシステム「ACHIEVE T800」にはコンパクトなオートローダーも設備。近い将来、印刷オペレータがプレート出力作業を担当し、さらなる省人化が期待できるとしている。
「1名だった製版部門の人員は、現在0.5名(半日)となり、この余剰を他の仕事へ振り分けられるようになった」(菊池課長)
「SONORA XTRA」への期待
同社では、間もなく最新バージョン「SONORA XTRA」のテストを開始し、8月からの完全移行を予定している。
「XTRA」は、無処理版の課題であった視認性や耐傷性を大幅に改良し、有処理版と同等のハンドリング性能を実現するとともに、感度を向上させ、プレートセッターでの出力生産性を高めるほか、省電力化にも貢献。さらにUV印刷での耐刷性も向上している。菊池課長は、XTRAへの期待について「視認性の向上」「省電力化」「耐刷性向上による予備版のさらなる削減」といった点を挙げている。
同社では版面での検版作業は行っていないが、視認性は「高いことに越したことはない」ということ。「同じシリーズの製品内でデザインの似ている案件については、版面の製品名・製品番号の確認が非常に重要である。その点、視認性の向上で確認作業が容易になる」(菊池課長)。XTRAでは、画像コントラストを飛躍的に高める新材料を導入したことで視認性が大幅に向上(従来比2.5倍)。さらに感光層を青紫色とし、有処理版に近い視認性を再現している。
一方、XTRAでは露光部の反応効率を高める新たな硬化システムを採用し、「感度」は理論的に約30%向上している。CTPでの生産性向上やレーザーパワーを抑えることで省電力に貢献する。
さらに、新デザインの砂目と新開発の高感度化された感光層の組み合わせにより、耐刷性はUV印刷で従来比1.5倍を実現していることから、予備版のさらなる削減が期待できる。
「刷版」という中間資材の変更で様々な経営メリットを享受している同社。今後も、より収益性の高い多品種小ロット印刷に軸足を置いた生産体制にシフトし、利益率の高い事業構造を構築していくことを最大の目標としている。目下の課題は、印刷工程の供給能力が高まったことで負担が大きくなっている後工程。とくに「抜き」の工程を設備・人員ともに強化していくという。また一方で、世代交代が進む中、技術の継承ととともに工程の平準化によるスキルレス化を同時に進め、人材確保、あるいはその先にある多能工化も進めていく考えだ。
「E段を使用している紙器・パッケージに対しては、G段に移行することで軽量化によるコスト削減、LED-UV印刷+刷版の無処理化による環境負荷低減などを積極的に提案し、新たな受注獲得につなげていきたい」(橘社長)
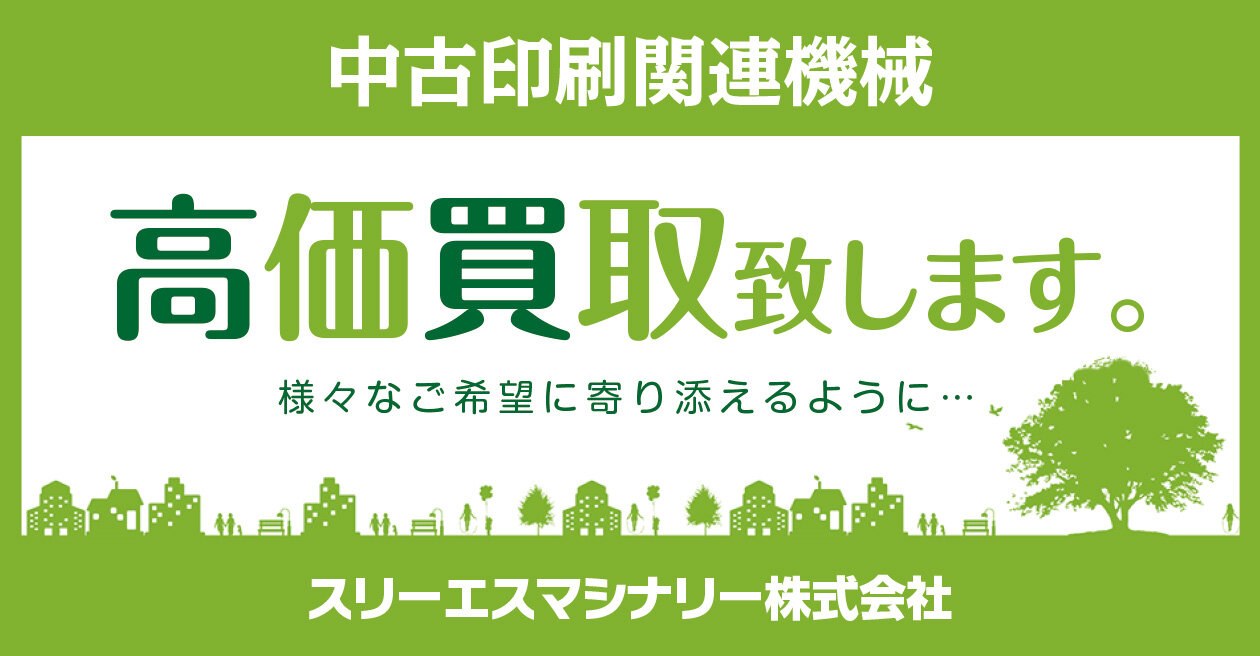